We use state-of-the art production, measurement, prototype and development equipment to meet your requirements.
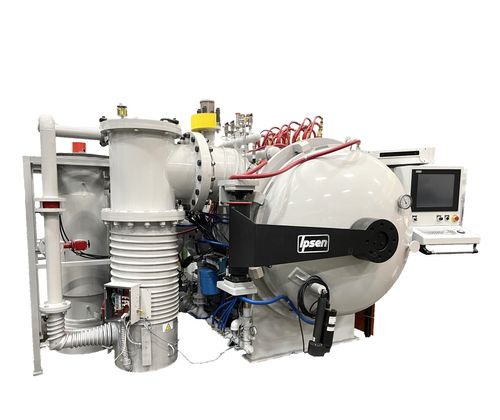
Metal heater and muffle furnace
To achieve even lower contaminated sintered parts production, metal muffle furnace from Ipsen has been deployed to our serial production line. Ipsen furnace has a long history and great experiences in heat treatment for aerospace or aviation industry, which requires a strict contamination control. Highly controlled heat and atmosphere in a hot zone system will provide quality sintered parts, and it maximises our μ-MIM technology USPs.
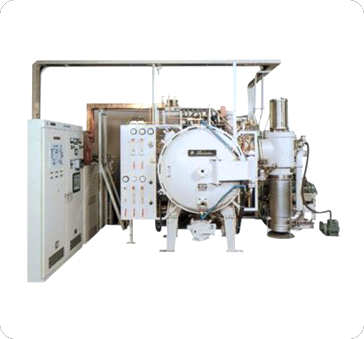
Sintering furnace
We use batch-type high-vacuum furnaces that allow a continuous degreasing and sintering process.

Bi-colour injection machine
By using a bicolor injection molding machine, we are able to inject a component with different metal materials or layered components.
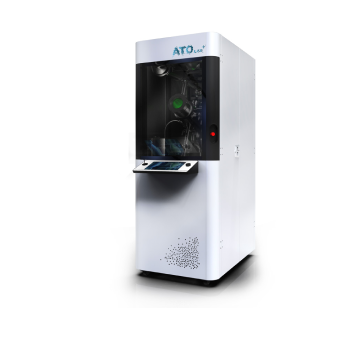
Metal powder atomizer
ATO Labo Plus is an evolutionary atomiser that allows manufacturing of metal powder in a laboratory environment. It is an ultrasonic atomiser to create metal powder from metal wire or a rod, which makes it possible to manufacture round powder suitable for the additive manufacturing technology.
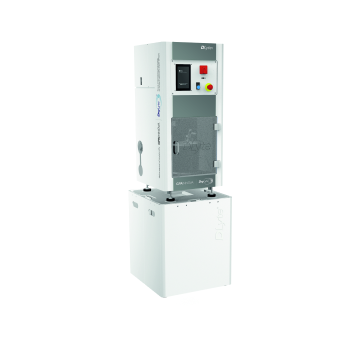
Dry electropolishing machine
It is an innovative equipment, which does not use any liquid, although it is an electropolishing equipment. This device allows the components to keep sharper edges compared with conventional electropolishing processes. As all the processes are automated, the operator does not require any special knowledge/skill. The substance used does not contain any harmful matter, which indicates that this device is simple and green.
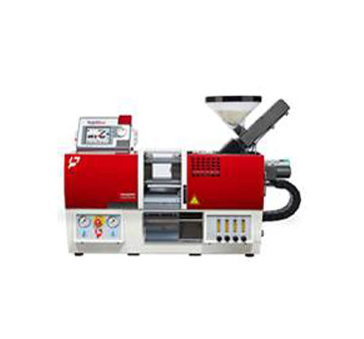
Small injection moulding machine
For the study of new alloy and special powders, a pellet wetting/injection molding machine for samples weighing 10 g or less and a compact molding machine for material up to 500 g have been introduced.
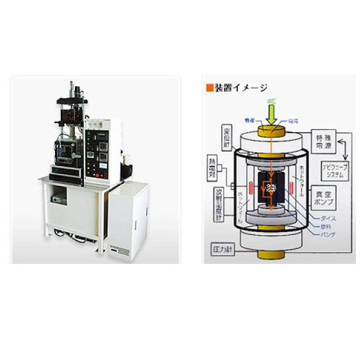
Spark plasma sintering (SPS) furnace
We use a SPS furnace for studying spark plasma sintering methods. With it we produce sintered parts in a short time.
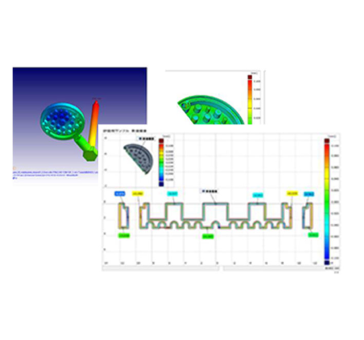
Custom flow analysis simulation software
TAISEI KOGYO, in collaboration with a MIM flow simulation software company, has developed a software for high-speed, high-precision analysis of MIM components, since conventional plastic flow simulation software was insufficient.
Evaluation equipment
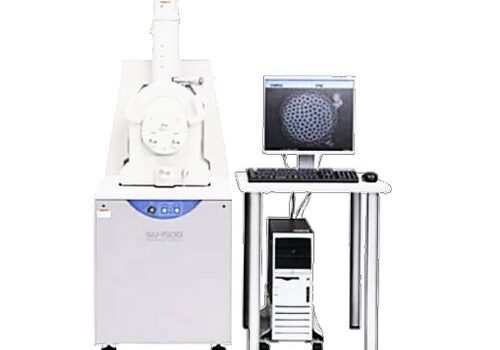
Scanning electron microscope
Used to observe the sample surface at high magnification by detecting secondary electrons and/or reflected electrons. An energy dispersive X-ray analyzer is attached.
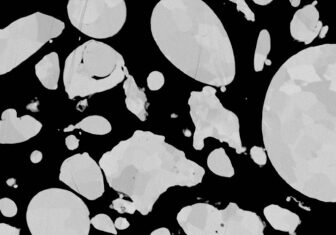
Energy dispersive X-ray spectroscopic device
An elemental analysis device that detects characteristic X-rays of elements irradiated with primary beam electricity or X-rays. It is integrated into the SEM system.
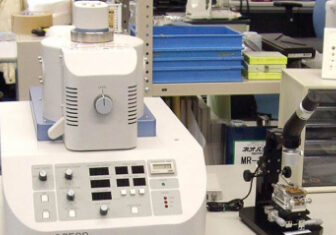
Ion milling
A flat measuring cross-section is processed with an argon ion beam.
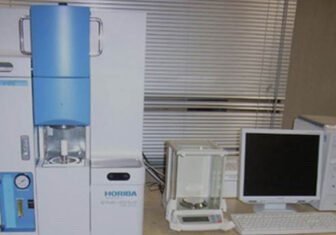
Carbon analyser
The amount of carbon contained in the sample is measured with high accuracy.
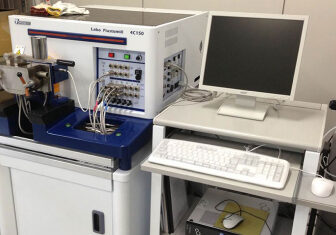
Viscosity measuring
The viscosity of the MIM feedstock is measured using MFR measurements, equipment for evaluating kneadability and equipment for evaluating flowability.
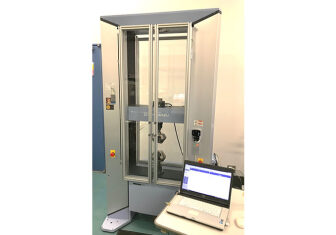
Universal testing machine
The most common equipment for tensile, bending and compression tests on metallic materials. We manufacture and measure specimens from new alloys and evaluate modulus of elasticity, Poisson's ratio, yield strength, etc.
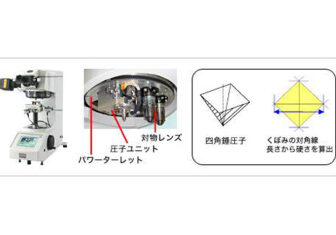
Hardness measuring
We use a micro Vickers hardness tester to evaluate our fine metal parts.
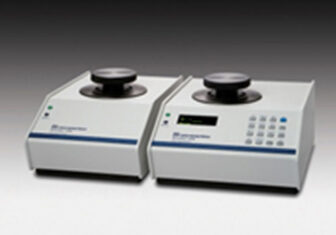
Pycnometer
We use automatic density meters to measure density.
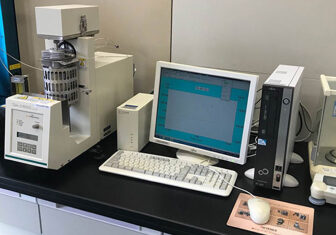
Thermogravimetry
We use a high-temperature thermogravimeter with a suspended design. It is also able to analyze in vacuum.
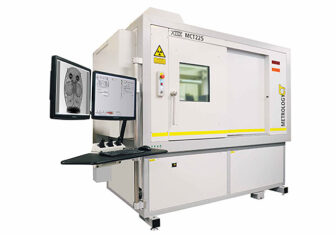
X-ray CT
We use an X-ray CT system with high measurement resolution.
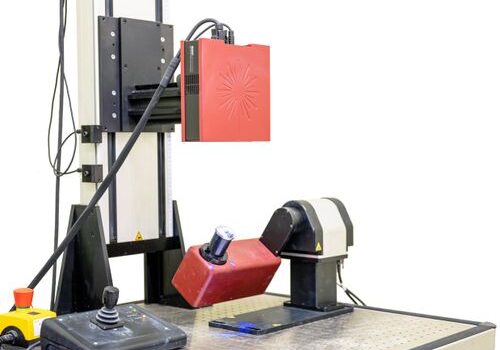
Optical 3D measurement
We use a 3D measuring system with the highest resolution in optical terms.
Schedule a free initial consultation with one of our experts
We will gladly answer your open questions and show you how we can help you solve your technical challenges.